面実装部品(SMD)のトランジスタを使ったダイヤモンドバッファ回路の基板モジュールを作ってみました。
電子工作の定番とされていた東芝製トランジスタ2SC1815、2SA1015も既に生産中止になっています。(秋月ではセカンドソース製は手には入りますが…)
ですが、2SC1815、2SA1015のチップタイプである2SC2712、2SA1162はまだまだ健在です。
今回は、それらを使ってみたかったので面実装トランジスタの使える基板を作ってみました。
回路図
回路図は下記になります。
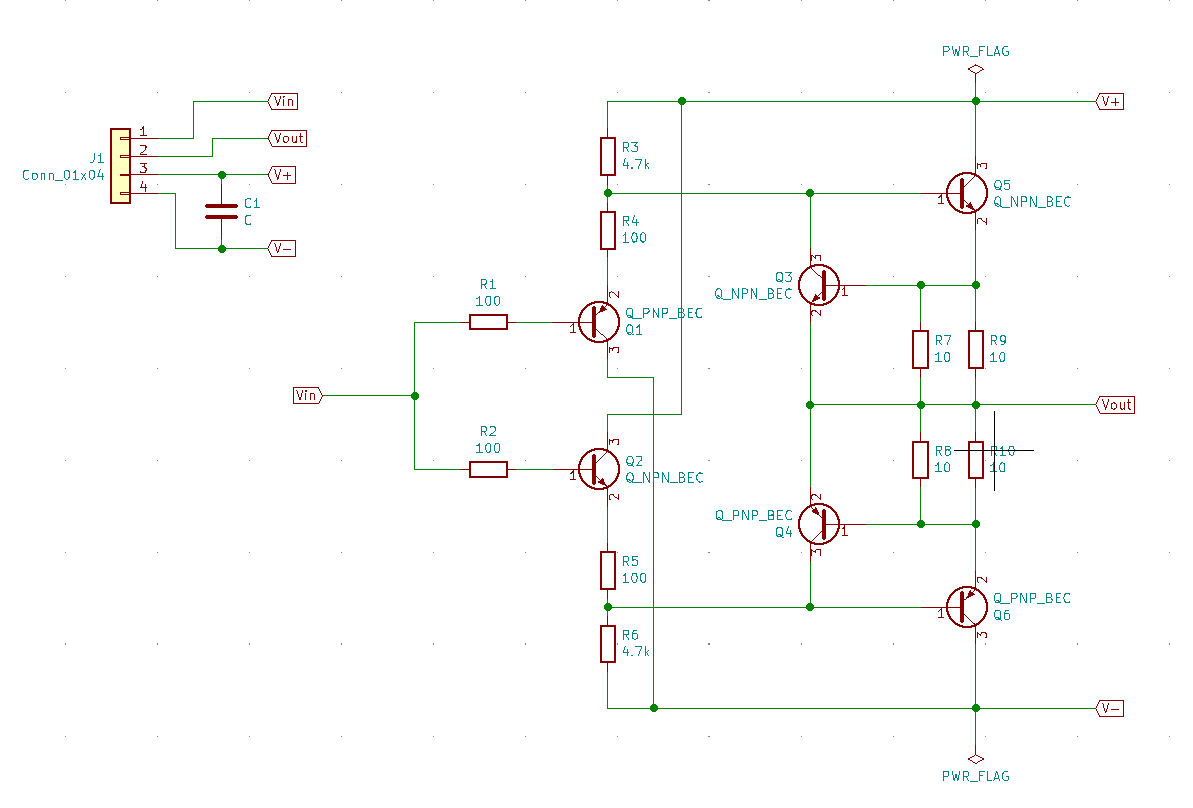
参考にした回路:トランジスタ技術 2010年12月別冊付録、定番回路集55 P22より
オーソドックスなダイヤモンドバッファ回路です。
Q3、Q4は出力の電流を制限するための保護回路です。
部品リスト
品名 | 参照名 | 数量 | 数値・仕様 | 備考 | 購入先(コード)※例 |
抵抗 | R1, R2, R4, R5 | 4 | 100Ω | 1608サイズ | 共立電子 ABM36Q |
抵抗 | R3, R6 | 2 | 4.7kΩ | 1608サイズ | 共立電子 ABO36V |
抵抗 | R7, R8, R9, R10 | 4 | 10Ω | 1608サイズ | 共立電子 ABM362 |
コンデンサ | C1 | 1 | 0.1µF | 3216サイズ | 秋月電子 P-15180 |
PNPトランジスタ | Q1, Q4, Q6 | 3 | 2SA1162 | BEC配列 SC-59(TO-236MOD) | 秋月電子 I-02702 |
NPNトランジスタ | Q2, Q3, Q5 | 3 | 2SC2712 | BEC配列 SC-59(TO-236MOD) | 秋月電子 I-00761 |
ピンヘッダ | J1 | 1 | – | 4端子、ピッチ2.54mm 今回はL型で製作 | 秋月電子 C-01627 |
トランジスタが面実装品なので、その他の抵抗等もチップ部品で作ることにしました。
チップ抵抗は共立電子で少数単位で買えます。送料もサイズが小さいものはネコポスが可能なので安いです。
沢山使う見込みがある抵抗は秋月電子でリールで買ったほうがお得かもしれません。(私は一生使いきれませんが買いました…)
※同じパッケージサイズの2SC3325、2SA1313でも作ってみたいと思います。
シミュレーション結果
事前に無料の回路シミュレーションソフトであるLTSpiceでシミュレーションしてみました。
実績のある回路ですが、いきなり基板を作るので、最低限シミュレーションで確認しておいた方が良いですね。
本当はブレッドボードとかで事前に試作したらもっと良いと思いますが、自分の場合それをやると満足して終了してしまいそうですw
オペアンプの非反転増幅回路の出力に挿入した状態でシミュレーションしています。
※トランジスタはデフォルトで入っていたRohmのモデルを使っています。
左上のグラフは入力電圧0.5V、出力電圧約2.5Vの波形です。ちゃんと増幅出来ていますね。
左下のグラフはQ6に流れる電流の波形です。
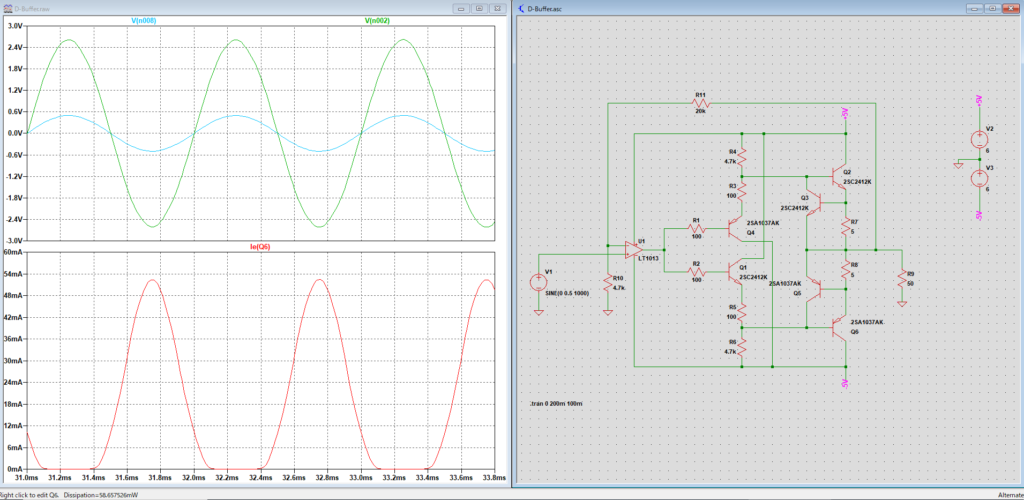
電源電圧を上げ過ぎるとトランジスタの消費電力(コレクタ損失)が上昇するので危険です。±5V程度までにしておいた方が良さそうです。
下の図で、左上の波形がQ6の消費電力(コレクタ損失)です。2SC2712、2SA1162のコレクタ損失の絶対最大定格は150mW(25℃時)です。
実使用でどのくらいの負荷が掛かるか判りませんが、発熱によるディレーティングも考慮しないといけません。小型のチップ部品なので余裕が無いですね。TO-92(コレクタ損失400mW)の2SC1815、2SA1015で作りたくなってきました。
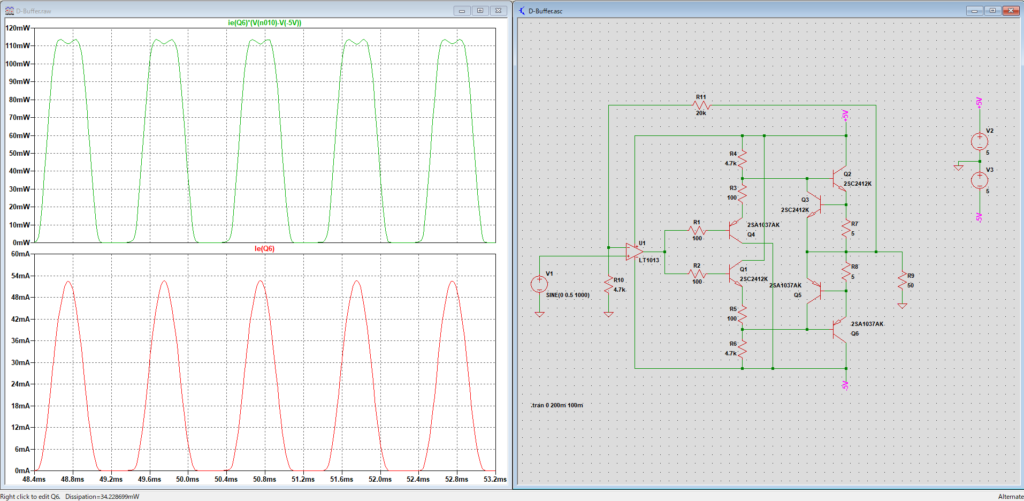
±6Vで50Ω負荷の場合、コレクタ損失のピーク値は150mWを超えてしまいます。
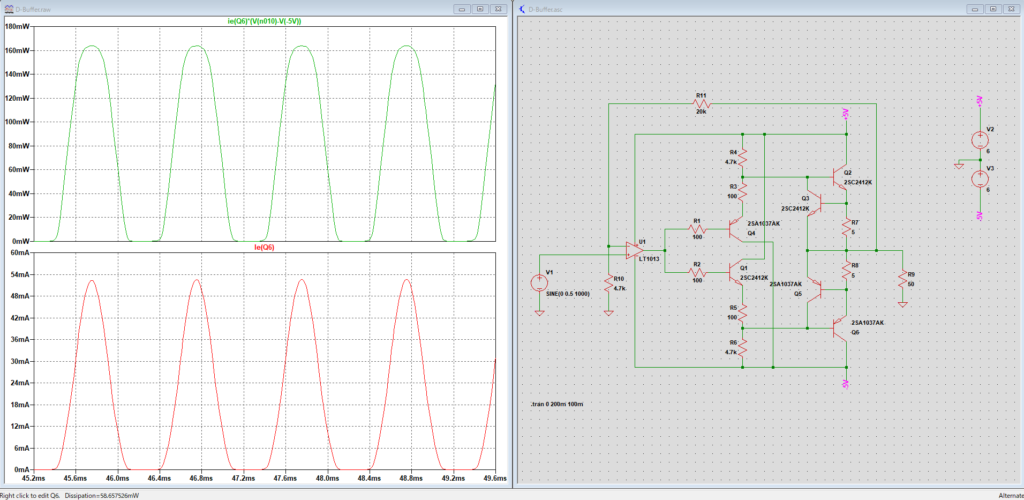
RL=10Ωの時のシミュレーション結果です。約110mAで電流制限が効いていることが確認できます。
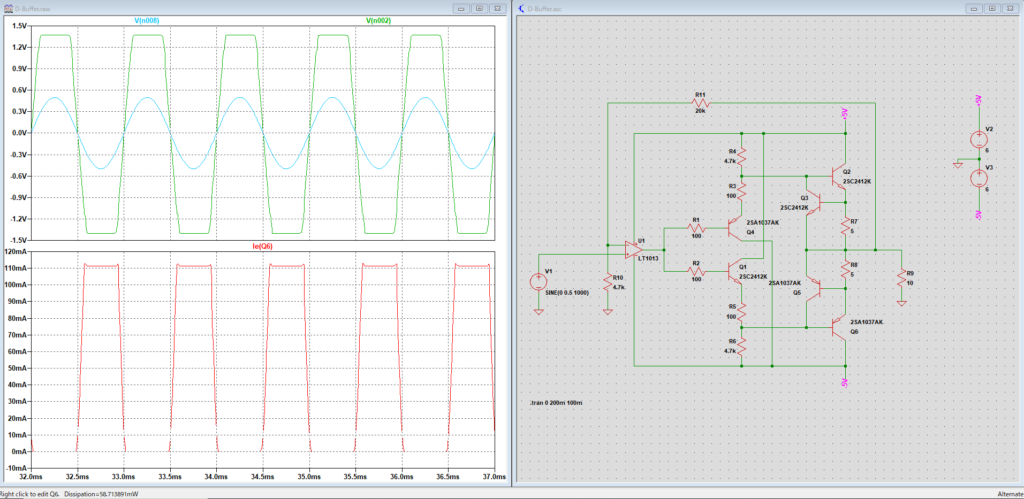
製作した基板
今回もフリーソフトの基板CADである、KiCADを使って基板を設計・製作してみます。
完成予想3D図
2.54mmピッチのカードサイズで、ユニバーサル基板やブレッドボードに刺して使うイメージで作りました。バッファカードとでも呼びましょうか。
基板サイズは33mm×20mmです。
あまり小さくない?気もしますが、気持ち放熱用ということで余白をベタにして残しました。チップ部品を使いたいのが目的ということで、今回はこれでよしとしましょう。
部品配置図
面付け(パネライズ)して発注してみる
今回も中国の基板メーカーであるElecrowに発注しますが、基板サイズが小さいため面付けして発注してみました。
Elecrowの仕様より、Vカットする際の基板寸法は80mm×80mm以上にする必要があります。
基板サイズは33mm×20mmなので、縦3枚×横5枚でギリギリ100mm×100mmに収まる算段です。
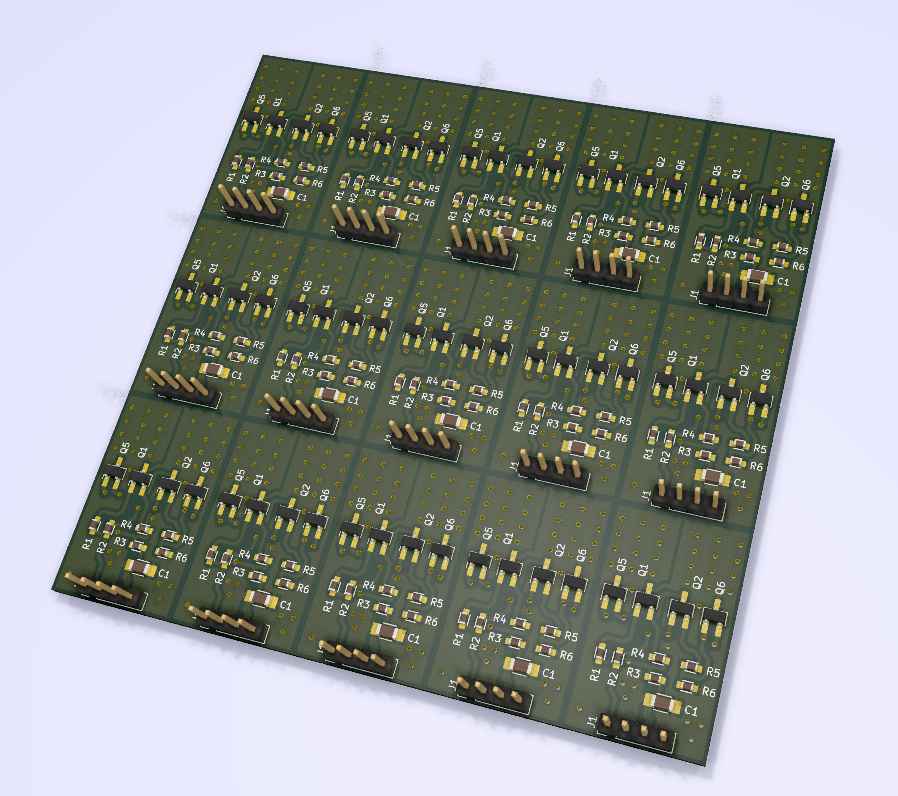
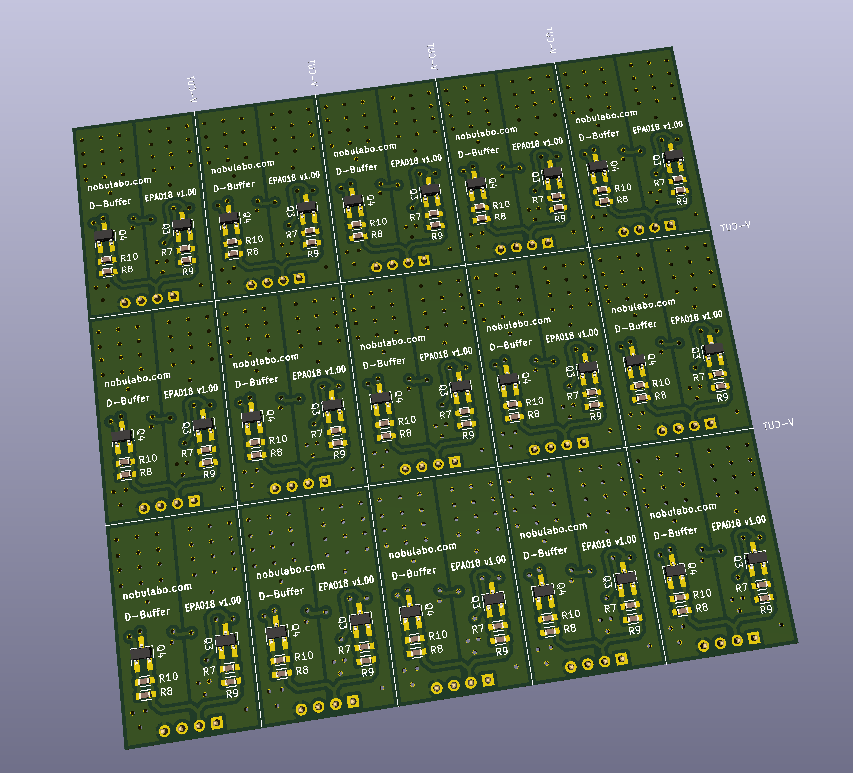
シルクの直線はVカット部を指示しています。
基板1シートで3×5=15個、10シート注文したら150個分出来ることになります。
そんなに作ってどうするんだ…とは思いますが、プリント基板の量産効果はすごいですね。
今回の基板の料金と送料は下記にまとめました。
届いた基板
到着した基板がこちらになります。レジスト色は黄色です。
今回の板厚は1mmにしてみました。
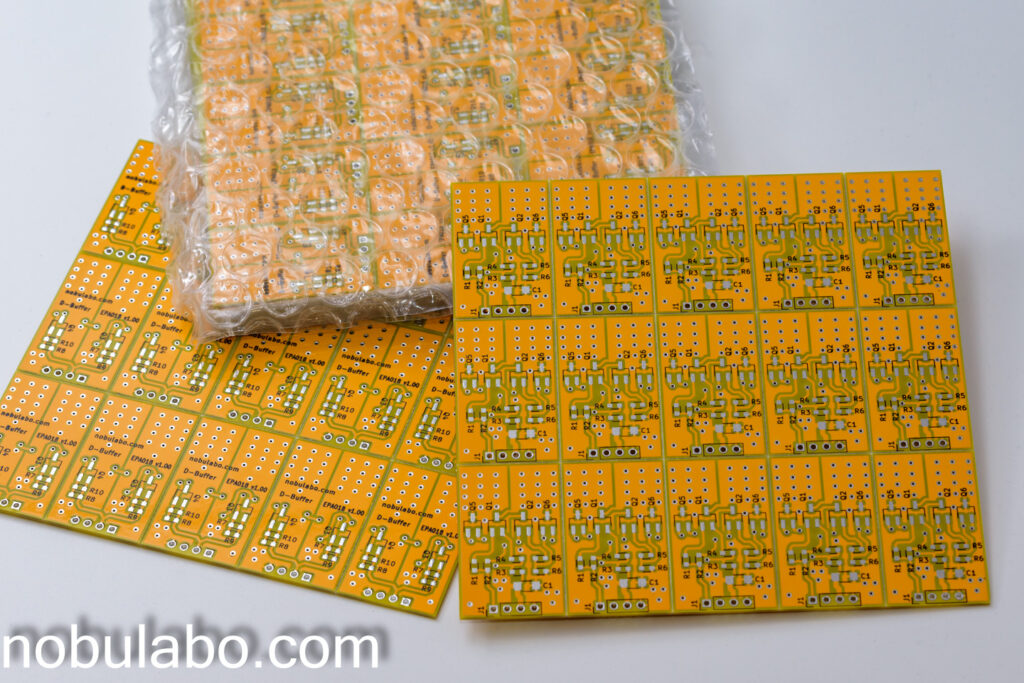
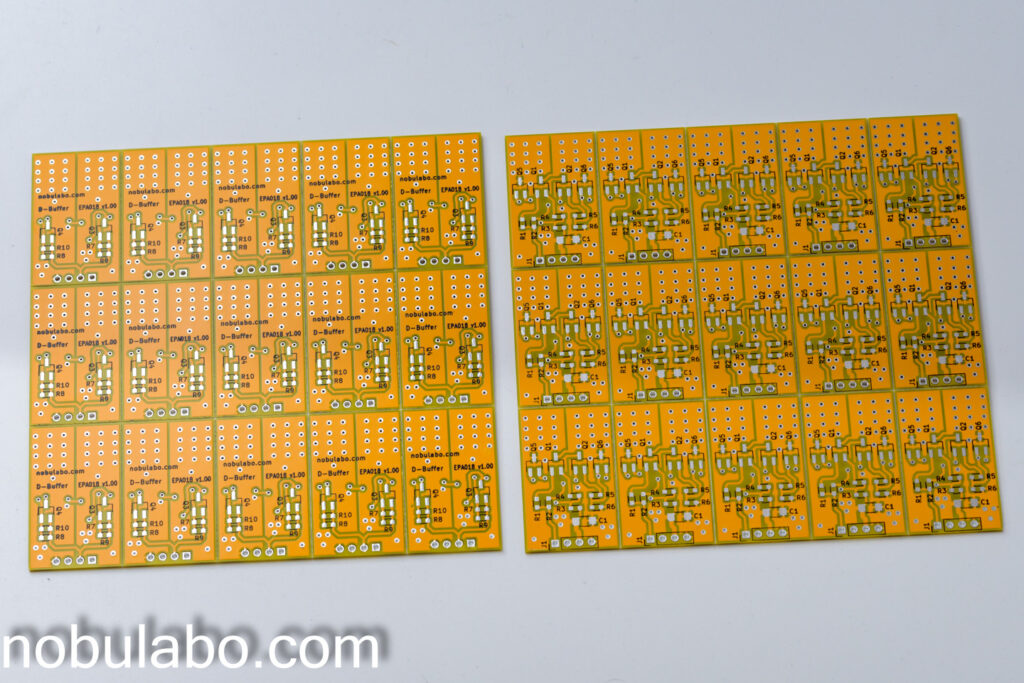
QRコードを入れる隙間がありませんでした。
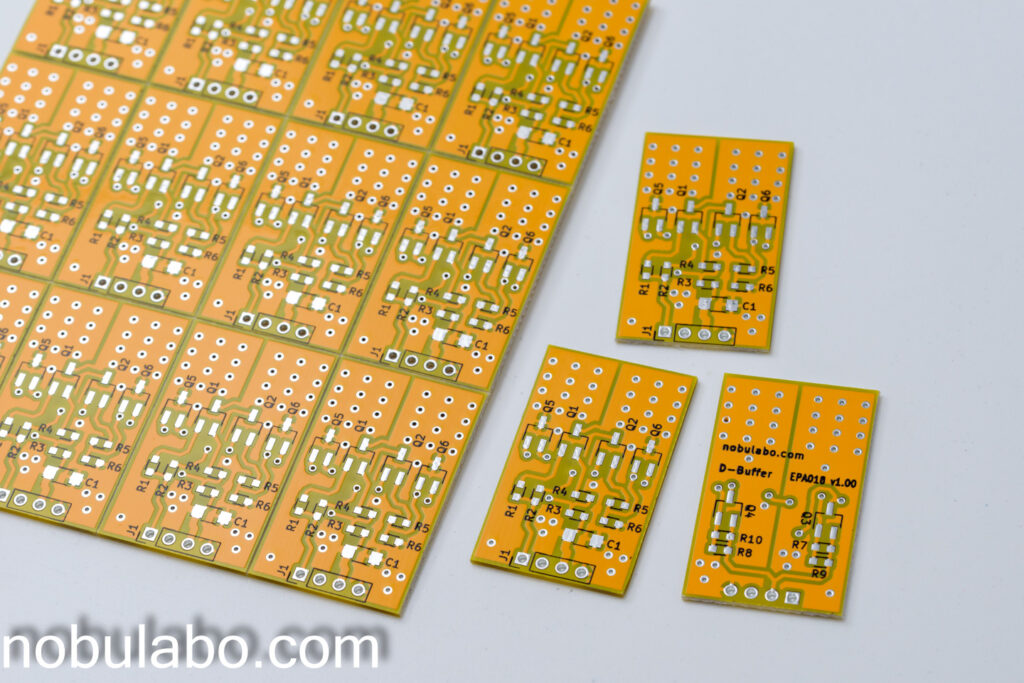
判ってはいましたが、マジで150個分の基板が届いてしまいました。
引き続き、製作と動作確認を行います。
続きは下記のページにまとめました。